|
Metal Casting Processes in China
Some clients wanted us to introduce the
main metal casting processes in China, then herein, we make a brief
introduction to their characters, differences and applications.
1. Sand Casting Process
Sand casting processes mainly include
green sand,
resin sand casting, and
shell molding process. The
green sand casting processes include manual green sand molding,
molding machine, and automatic molding line.
Sand casting processes are
very common in China, most of metal foundries are mainly using sand
casting processes to produce metal
castings. These processes have low production costs, simple
technical requirements, and high production rate. So,
sand casting foundries are the most common process in
China.
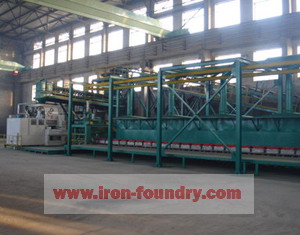
2. Metal Mold Casting Process
Metal mold casting process is not common in China, only few metal
foundries are using this process. Although the
metal patterns are heat
resisting metals, they can not bear too high temperature, so only
can produce some metal castings with lower melting temperature, such
as aluminum, zinc or bronze castings.
The shortage of metal mold casting process is low production rate,
but advantage is good surface quality, and less
casting defects,
especially no sand holes.
3. Lost wax investment casting process.
Lost wax investment casting process mainly includes two types of
materials, one uses water glass, another uses silica solution as the
bonding material. All these two casting processes will need to use
the yellow wax.
Investment casting process normally has been used to produce
steel
castings, especially small steel castings. They are not suitable to
produce large castings because of the strength of bonding materials.
The advantages for this process are the good surface quality,
accurate dimensions and less casting defects, but the disadvantages
are their high production costs and pollution of production.
In China, the investment casting foundry is reducing, especially in
South of China, some foundries are trying to replace this casting
process by shell molding process.
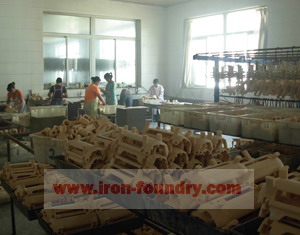
3. Lost Foam Casting Process
This process need to use metal pattern to make foam molds, then
during pouring hot iron, the foam will be melted, then the iron will
become the same shape as the foam.
This process is suitable to produce large iron castings, they could
reach better surface quality and demand few workers. However, its
technical problems are not few, so there are few foundries who could
use this process very well.
4. Die Casting Process
Die casting process is press the hot liquid metals into a metal
mold, then after cooling, the metal castings will be made.
This process normally produces high precision aluminum and zinc
castings. The size and weight normally are small and light. Most of
them will be used for automotive industries.
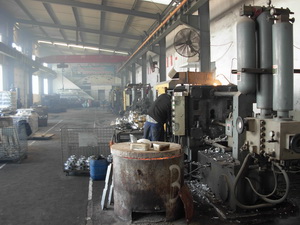
5. centrifugal casting
process
This process normally produces cylindrical castings, and not common
in China. There are only few foundries using this process.
The advantages of this process are less casting defects, but
disadvantages are shape limitation and high pattern costs.
6. continuous casting process
This process mainly produces long tubes,
plates and rods. It is not very common in China, so only few
iron foundries could use
this process.
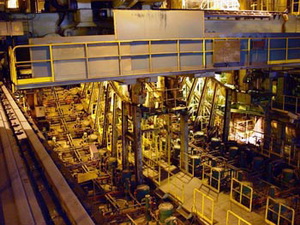
Home |
More Articles |
|