Why are castings popular in modern industry? This is because of the functional and economical advantages of castings.
When you stop to think about the forming of a rough component, the most obvious reason to choose the casting process over other processes is it's the most simple and direct method to obtain a near net shape component for further processing. One of the foundational concepts of casting design is that you can put the metal where you need it.
For example, in a welded fabrication, tapered material cross sections to reduce stress risers are difficult to make, whereas a casting design can add these features at no cost. Fabrications often require the use of double plates to change material thickness which can be unsightly. Castings can add material thickness, while still maintaining the aesthetics of the part.
Conversely, the designer can remove metal from a part where it isn't needed. One example of this would be the use of cores to lighten or remove metal sections where modeling indicates areas of very little or no stress. Employing this strategy usually results in the development of a casting design that should look different from the initial concept and can potentially offer a significant weight reduction. Based on the cost of the material, the weight reduction can offset the cost of the core and translate into an overall cost savings on the component.
Additional weight reductions can come from changing cast material types. For instance, if you have the ability to change your part from steel to ductile iron, you will automatically see a lower casting weight since ductile iron has density that is about 10% lower than steel.
An industry best practice is to use the casting process to redesign several components that are bolted together into a one-piece casting. This allows the designer to eliminate bolted joints and the problems that go along with them, such as leaks and fit-up issues. Overall reliability and dependability of the one-piece casting can increase, providing increased customer satisfaction. Combining multiple parts can also improve assembly times and reduce the amounts of various fasteners and hardware, thus simplifying inventory. In addition, the amount of assembly floor space could be reduced when multiple parts are combined into one piece.
Designers are also reaping the benefits of employing various casting processes to either eliminate or significantly reduce machining. Let's take a quick look at the capabilities of the investment casting process to illustrate this concept. Because the pattern used for an investment casting is actually a highly accurate wax part molded in a machined tool, some features that have traditionally been machined can be obtained in the as-cast state. An example would be clearance holes for screws or bolts that can be cast instead of drilled. Added benefits include minimized (or potentially eliminated) draft, very tight piece part tolerances, and excellent surface finishes.
The size of a part is not a limiting factor for castings. The adaptability of the process can allow for making parts that weigh as little as several grams to over several hundred tons. The casting process also offers freedom in the quantities that can be made; small prototype orders or large production lot sizes aren't a problem.
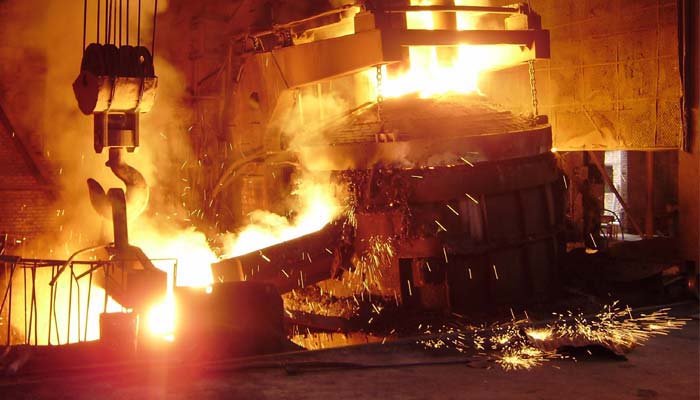 |