Shrinkage defects are very harmful for iron and steel castings. Let us discuss how to prevent shrinkage defects during production.
Shrinkage defects appear because metal alloys shrink as they cool. It is normal for an alloy piece to shrink as it solidifies (which should be included in calculations when designing the mold). However, defects occur when the metal shrinks unevenly, causing it to either distort the shape of the final product or create interior holes. This can also stress the metal.
Open Shrinkage Defects
Open shrinkage shows up on the surface of a cast product either as a dip (also known as a caved surface) or a hole (also known as a pipe). When metal shrinks unevenly, it draws air inside the mold in that area to create these types of defects.
Closed Shrinkage Defects
Closed shrinkage appears in the form of holes inside of a casting, generally where a part of the liquid metal was hotter than the rest of the material. It can appear in macro or micro form. Micro shrinkage, also called shrinkage porosity, looks to the naked eye like jagged marks or lines. The holes, which look angular, can only be seen with a microscope.
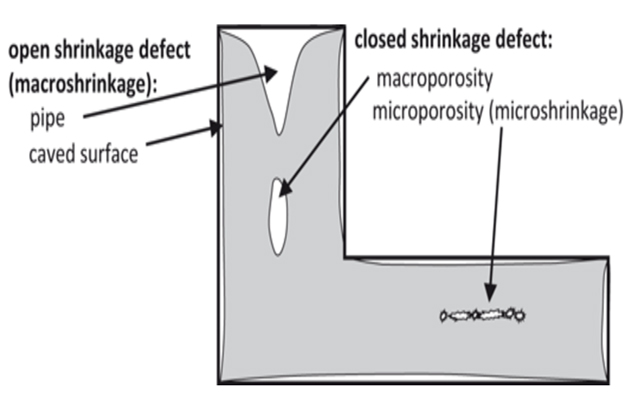
Warping
Warping can happen either during the metal's solidification or afterward, changing the casting's dimensions and shape. This stresses the metal and causes curving, especially in large and flat sections of castings.
What Causes Shrinkage Defects?
Shrinkage defects show up when the liquid metal in the mold is not all the same temperature. There are two possible causes for this: either the metal being poured into the mold is too hot or the metal is solidifying unevenly. Uneven solidification often happens when mold design ignores the rule of directional solidification. This rule states that the thinnest pieces of the molded shape should solidify first, and the thickest pieces solidify last, to ensure shrinkage doesn't alter or damage the piece.
How to Prevent Shrinkage Defects?
Problems with continuous flow at the right temperature (which contributes to uneven solidification) can be lessened by ensuring a continuous, even supply of liquid metal into the molds. This can be accomplished by using a runner and gate system with risers to supply the molten metal, which involves channels for the metal to flow through into the mold (the running system) and reservoirs of liquid metal on top of the mold (also known as risers) to fill in where the metal shrinks.
Additionally, molds can be given padding, which widens the ends of narrow pieces attached to thicker parts, as this helps ensure the thicker sections get enough liquid metal before the thin part solidifies. Some manufacturers also place cooling ribs, cooling coils, or chills inside the molds to disperse heat faster. Pouring the metal at a lower temperature may also help.
Warping specifically can be avoided by using heat treatment for iron alloys, which removes leftover stress. For aluminum alloys, straightening the casting between the quenching and aging processes avoids warpage. It can also prevent warping to ensure large areas have more of a ribbed shape, like corrugation, to make a piece cool more evenly.
|