There are various types of casting processes. They have their own benefits and disadvantages.
Below, you will find the different casting processes, each with its advantages, disadvantages and recommended application.
Investment Casting
Also know as lost wax casting, investment casting is a process commonly applied in cases where both solid parts and complex, hollow cores are required.
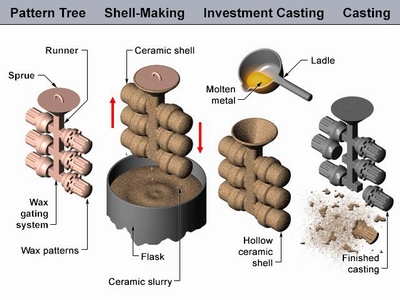
Advantages
1. It is able to deliver close dimensional tolerances.
2. Both ferrous and non-ferrous metals can be casted using investment casting.
3. It delivers a good as-cast finish.
4. With investment casting, complex shapes, intricate core sections, finer details and thinner walls are possible.
5. It offers a flexibility in design and is a useful process for casting alloys that are difficult to machine.
Disadvantages
1. Investment casting has a higher cost associated with it. In fact, it is more expensive than sand casting, permanent mold and the plaster casting process.
2. When compared to other types of casting processes, investment casting needs a longer product-cycle time.
3. There is a limitation on the size of parts that can be casted.
4. The advantages of this casting process overshadow costs when permanent mold and sand casting cannot deliver the desired complexity needed. Costs are also reduced by the quality surface finish investment casting delivers, reducing the cost of both machining and tooling.
Sand Casting
A process typically relying on silica-based materials, sand castings process involves finely ground, spherical grains tightly packed together into a smooth molding surface.
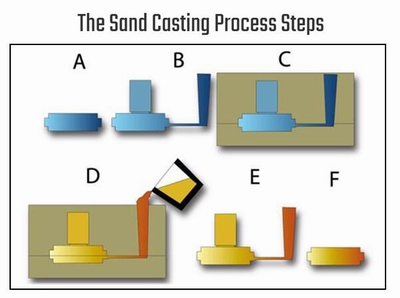
Advantages
1. This is the least expensive process when producing small quantities (normally less than 100) and also boasts with the least expensive tooling.
2. With sand casting, manufacturers are able to cast very large parts.
3. Both ferrous and non-ferrous metals can be casted using this process.
4. A low post-casting tooling cost.
Disadvantages
1. Sand casting's dimensional accuracy is less than that delivered by other processes.
2. This process requires large tolerances.
3. The surface finish for ferrous casts delivered by this process usually exceeds 125 RMS.
4. Castings produced with this proceed usually exceeds the calculated weight.
Die Casting
Die casting involves the molding of materials under high pressure, and consists of Cold-Chamber Conventional Die Casting, Hot-Chamber Conventional Die Casting and Multi-Slide Hot-Chamber Die Casting for aluminum, brass, magnesium and zinc.
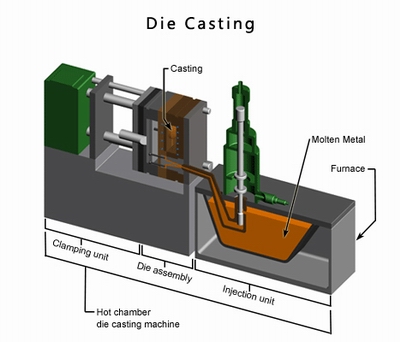
Advantages
1. Die casting is able to deliver parts that has a good dimensional tolerance.
2. Parts produced using die casting require a minimal amount of post machining.
3. This casting process also delivers an excellent part to part consistency, ideal for large production scales.
4. It is a cost effective process when used for a high volume production run.
5. This process is suitable for metals with a relatively low melting point, such as aluminum, lead, magnesium, zinc and some copper alloys.
Disadvantages
1. This process is only an economically sound option for a large production quantity, as the tooling costs for die casting are expensive.
2. In this process, it is difficult to guarantee minimum mechanical properties and is thus do not function as structural parts.
3. This process is also not recommended for hydrostatic pressure applications.
4. There is a limit on the size of parts that can be casted. It is a suitable process for castings of about up to 75 pounds.
While it is an economically viable option for large production runs, die cast parts' mechanical properties cannot be assured, resulting in these parts not having a structural function. It is however a good process to opt for in cases where a large quantity of the part is needed, the parts produced will not have a structural function and in cases where parts will not be subjected to hydrostatic pressure.
Permanent Mold Casting
Permanent mold casting is a process used in which permanent molds consists of mold cavities, machined into metal die blocks and appropriate for repetitive use.
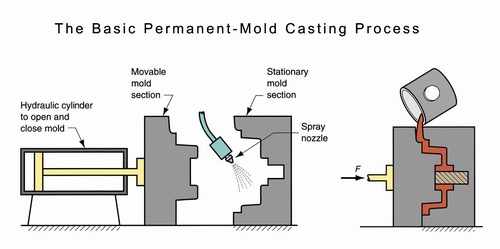
Advantages
1. This type of casting process is less expensive than die casting or investment casting.
2. Casting delivered using this process are dense and pressure tight.
3. Permanent mold casting is able to deliver a closer dimensional tolerance than sand casting is able to.
4. The repeated use of molds are possible.
5. It has a rapid production rate combined with a low scrap rate.
Disadvantages
1. This process is only able to cast non-ferrous metals.
2. Permanent mold casting has a higher cost of tooling than sand casting has.
3. It becomes less competitive with sand casting in cases where three or more sand cores are required in the process.
4. Because of the high tooling cost associated with permanent mold casting, it is only a financially viable option for high production runs.
5. Limited to small castings with a simple design exterior.
These types of casting processes are used in cases where parts are subjected to hydrostatic pressure and is perfect when casting parts that have no cores, a low profile and is part of a large production run (usually more than 300).
Plaster Casting
Plaster casting is a casting process with similarities to sand casting. Instead of using sand in the process, a mixture of water, gypsum and strengthening compounds are used.
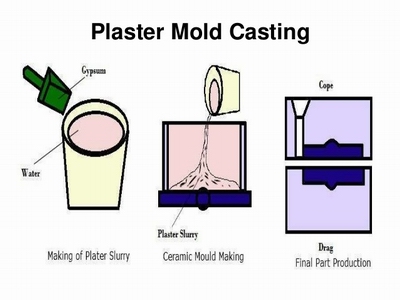
Advantages
1. Plaster casting is capable of delivering a closer dimensional tolerance than sand casting is able to.
2. It delivers a smooth, as-cast finish.
3. Casting larger parts using this process is less expensive that it would be when using investment casting processes.
4. Intricate shapes with finer details are possible.
5. Thinner, as-cast walls are also delivered by this casting process.
Disadvantages
1. Plaster casting requires a minimum of a 1 degree draft.
2. It is a more expensive process when compared to permanent mold and sand casting.
3. This process may require the frequent replacement of plaster molding materials.
Though a more expensive process than most sand casting processes, it is a more economically sound option when a good surface finish quality is needed.
|