|
Shell Molding Process VS Green Sand Casting
As for some complex or thin wall thickness
castings, we often suggested our customers to use shell molding
casting process, instead of green sand casting process. However,
some customers were confused about their difference, advantages and
disadvantages. Herein, let us make a brief comparison.
The main
differences of shell molding process vs. green sand casting
1. Different sand materials
Green sand casting process uses wet clay as the bonded material, so
its material cost is very low. However, shell molding process uses
phenolic resin as the bonded material, which will be more costly.
Green sand is black, and pre-coated resin sand is yellow.
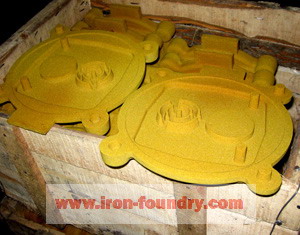
green clay sand
pre-coated resin sand
2. Different production costs
Shell molding process needs to use expensive pre-coated resin sand,
and needs to make sand molds by molding machines.
Therefore, its production cost will be higher than green sand
casting process. Normally, the iron castings made by shell molding
process will cause higher production costs 0.15 to 0.30 USD/kg.
3. Different tooling costs
Shell molding process needs to use metal patterns, because the
pre-coated resin sand needs to be baked at very high temperature in
molding machines. So, its tooling cost is comparatively higher.
Green sand casting process could use cheaper plastic patterns (also
called as epoxy resin patterns), and aluminum patterns. When making
samples, even wooden patterns could be used.

epoxy resin pattern
metal patterns for shell molding
The advantages and
disadvantages of shell molding process
1. Good surface quality and less casting defects
Shell molding castings have very high surface quality, good finish
smoothness, and less sand casting defects, such as sand inclusion,
air holes and sand drop.
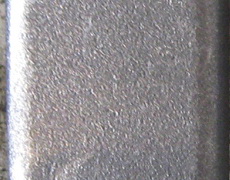
green sand casting surface
shell molding casting surface
2. Higher dimensional tolerance and
less straightness deformation
Because the pre-coated resin sand molds are a type of hard molds, so
the shell molding castings have very high dimensional tolerance.
Moreover, the iron castings could be cooled in the sand molds for
long time, so they will have less deformation of straightness and
flatness.
3. Suitable for complex structures and thin wall thickness
The strength of shell molds is higher than other sand molds, so they
could be used to produce the iron castings with complex inside and
outside structures, such as stove gas burners, manifolds etc.
Moreover, they could control the wall thickness very thin to 5.0 mm,
and make the wall thickness very uniform.
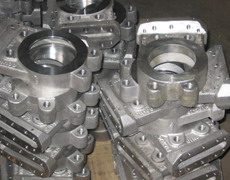
shell molding castings
4. High casting prices and tooling
costs
Of course, the disadvantages of shell molding process are high
casting prices, and tooling (metal pattern) costs.
5. Have limitation to casting weights and sizes
Because of the size limitation of shell and core molding machines,
this process is not suitable to produce very heavy and large
castings, such as over 500 mm long, or 30 kg weight.
The advantages and
disadvantages of green sand casting
1. Low casting prices and tooling costs
The largest advantage of green sand casting process is lower casting
prices and tooling costs. Especially, for large castings, the saving
for tooling costs will be very considerable.
2. Suitable for larger or heavier castings
The restriction to casting weight and size is comparatively few. So,
green sand casting process could produce small castings less than
0.5 kg/pc, and can produce large castings heavier than 300 kg/pc
too. The casting sizes could be from 20 mm to 2 meters.
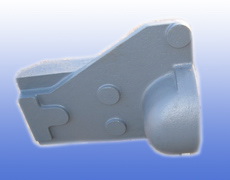
green sand castings
3. Worse surface quality and casting
defects
Its disadvantages are also very obvious. The surface quality is not
good, and sand casting defects will be comparatively more than other
casting processes.
However, it does not mean their surface quality can not be
acceptable. If the iron foundries use very fine sand, or use
automatic molding equipments, their surface quality will be good
enough for most of requirements.
4. Low dimensional tolerance
If the iron foundries use manual molding green sand, then the
casting dimensional tolerance will be lower than shell molding
process. However, if they use automatic molding machines with green
sand, the tolerance will be much better.
Summary
Both green sand casting process and shell molding process have been
widely used worldwide, so their own advantages are undeniable.
Normally, the iron foundries will suggest to use some suitable
casting process according to the casting weight, size, structure and
requirements. So, the customers should learn about their differences
to costs and casting quality.
Home |
More Articles |
|